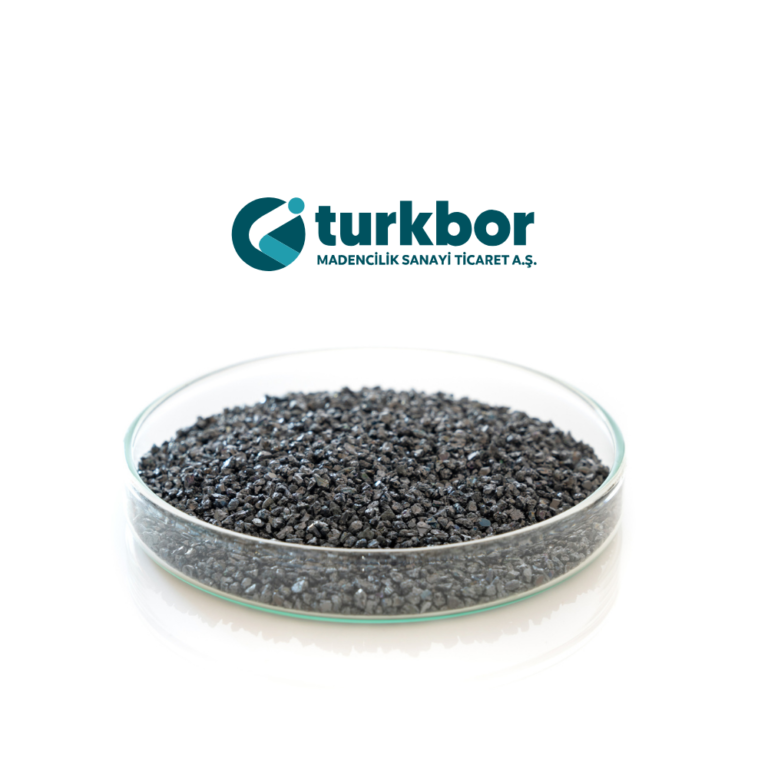
Boron carbide was first found in 1858. They prepared and defined their compounds named Joly in 1883 and Moissan in 1894, B3C and B6C, respectively.
Boron Carbide (B4C) which is shown among the new generation hard materials, belongs to the most important non-metal group and is the lightest and hardest material. Its production has been desperately needed lately.
The composition of commercial Boron Carbide is in a ratio of B: C = 4: 1. Boron Carbide (B4C) is an important Boron End product with a high market volume among hundreds of Boron compounds.
Boron Carbide has high hardness (300hv), low density (2.52 g / cm3), melting point (2447 0C), high elastic modulus (460 gpa), low fracture toughness (3.3 mpa.m-½) in ballistic applications. Its advantageous properties and strong resistance to corrosive effects have made Boron Carbide one of the indispensable elements of the new generation armor technology.
Boron Carbide is one of the hardest materials known after diamond and is used in the Refractory (Materials Resistant to High Temperature) sector as rocket propellant high energy jet fuel and rocket fuel in the aviation industry due to its ability to generate high heat with ballistic armor and Boron Carbide.
Boron Carbide
Import
Turkey, Boron Carbide in milled form, are imported from the USA, Germany and China.Technology producing companies and Boron users established in Europe and the USA do not transfer technology even though they buy Boron from our country. Chinese technology is not accepted by advanced world countries.
Boron Carbide armors, whose market share is growing day by day, can only be produced in 6-7 countries in the world. With Boron Carbide, vehicles, helicopters, military vehicles such as tanks and buildings are armored. This product is on boron chemicals produced in Turkey adds more than 100 times.
Boron carbide component has high hardness, excellent resistance to chemical and mechanical corrosion, excellent strength / weight ratio and high heat resistance due to its very low density (2.5 g / cm3) are produced.
Armor plates made of boron carbide, a high-tech ceramic raw material, are up to 70% lighter compared to other traditional armor materials, so boron carbide raw material is highly preferred in protective vests and armor manufacturing where lightness is very important.
In addition, boron carbide armor plates are used in tactical vehicles, light armored vehicles and helicopters where lightness and mobility are important. The purpose of armor solutions is to provide minimum load and maximum protection. High hardness, excellent resistance to chemical and mechanical corrosion, very low density, excellent strength / weight ratio and high heat resistance properties are the main reasons why B4C is preferred.
Ceramic armors made of raw material, also called boron carbide, are used as the basic material in new generation bulletproof vest plates. Boron carbide is used as abrasive grit or powder. Boron carbide and boron nitride; they are important compounds used as high temperature resistant (refractory) material in casting walls and as abrasive material in spraying.
One of the most common uses of boron carbide is its use in nuclear power plants for radiation protection purposes and as a fuel loading rod. Boron carbide loading bars are used in most of today’s nuclear power plants.
The neutron absorption ability of boron carbide stems from the boron isotope in its structure. The use of boron carbide in this field will continue to increase its importance, as the use of nuclear technology has increased.
Boron steels, boron carbide and titanium boron alloys are used in nuclear reactors. Stainless boron doped steel is preferred as a neutron absorber. Approximately each boron atom absorbs one neutron. For this reason, it is used in the control systems of atomic reactors, in cooling pools and in closing the reactor with alarm. Boron is unique in its ability to absorb thermal neutrons. It emits only a slight gamma ray and easily absorbs alpha particles.
Nowadays, it is used in every industry where high hardness and strength is required in the defense industry and in solid missile fuels.
ALTAY tank, which will be produced with 100% Turkish engineering in our country, will start mass production in the coming days. It has a feature that distinguishes it from other tanks that will make it the first in the world. This feature is the new armor technology produced with “Boron Carbide “.
Boron Carbide
Usage Area
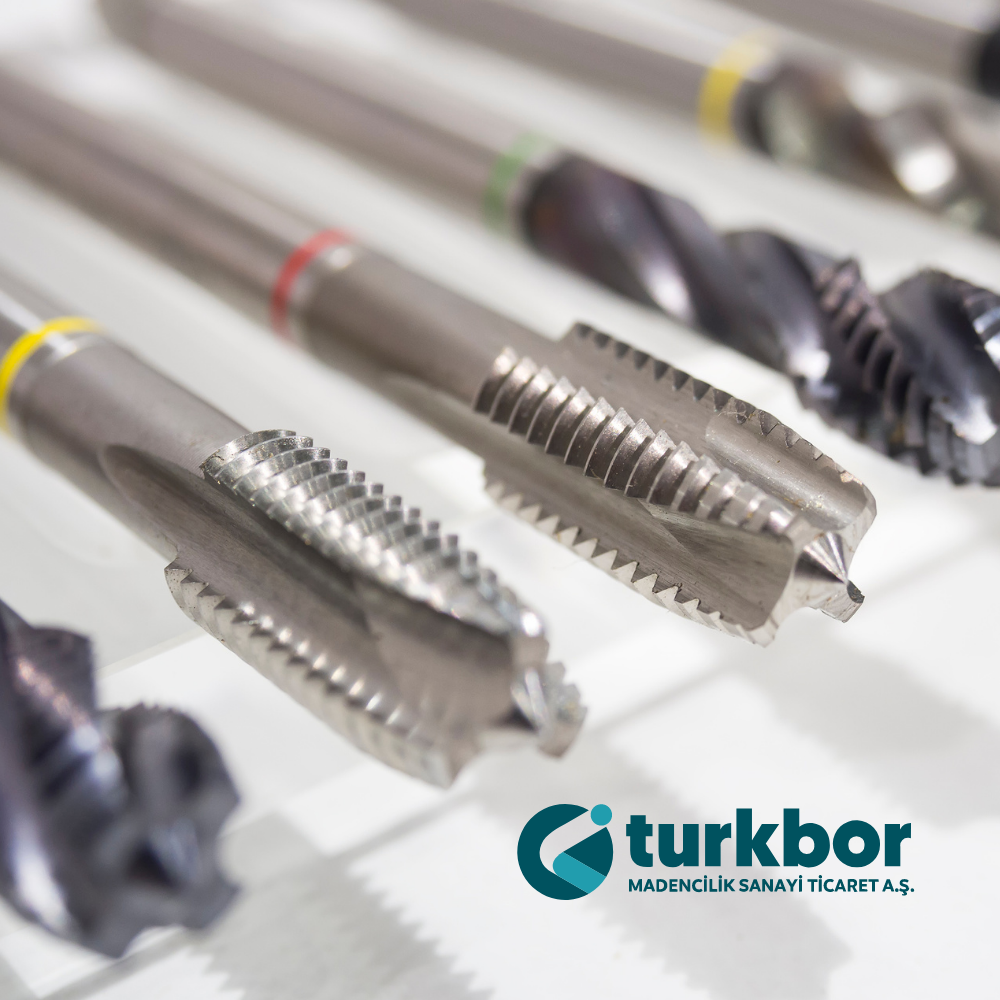
